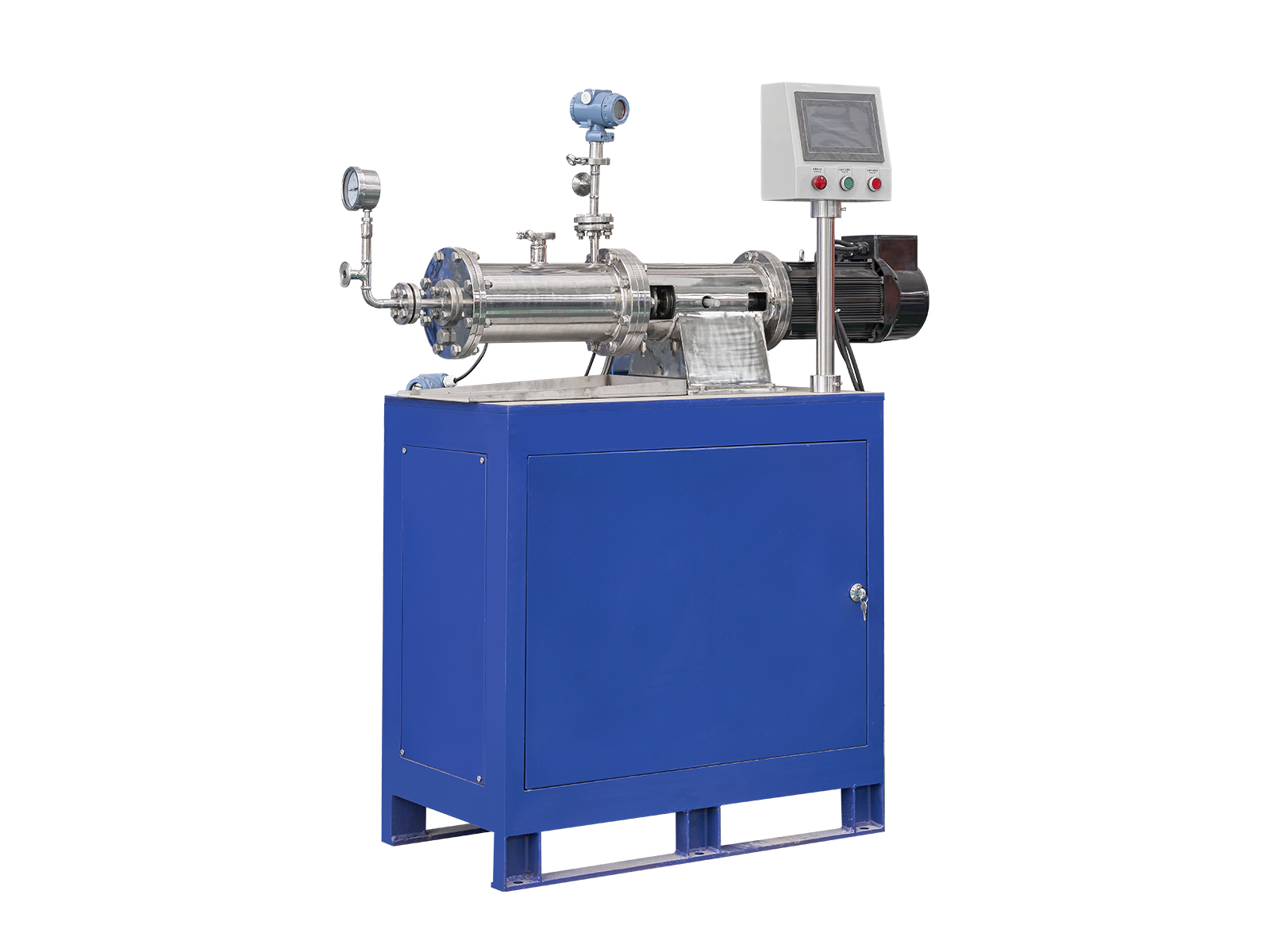
ALC Mill
ALC Mill
Model:
ALC mill is mainly composed of a grinding cylinder filled with grinding media and a rotary agitator.
The rotary agitator is equipped with 8 mixing plates and a product separator.
Eight independent grinding chambers are formed between the stirring plates, and the grinding media circulates in each chamber, so multi-stage grinding is formed. The stirring shaft rotates at high speed to stir the grinding media, resulting in impact, shear and friction, so that the material can be superfine comminuted. Under the centrifugal force of high-speed rotation, minerals and grinding media are distributed radially from the inner wall of the axial cylinder according to the particle size from small to large, so as to realize the selective grinding of "large grinding, small grinding".
The product separator at the discharge end has the function of internal classification, which can discharge the qualified products out of the mill, and leave the media and particles whose particle size does not meet the requirements in the mill for furthergrinding, so as to realize open circuit grinding, narrow particle size distribution of products and simplify the production process.
Feature 1
Feature 2
The discharge end of ALC mill is equipped with a product separator. The qualified products are discharged from the central area of the mill. The media and particles whose particle size does not meet the requirements are returned from the edge of the cylinder to continue grinding. Thus, the closed circuit classification effect is realized and the production process is greatly simplified.
Feature 3
During the grinding process, the electrochemical reaction between sulfide minerals and iron grinding media results in the corrosion of grinding media. The adsorption or deposition of iron oxides or hydroxides formed by corrosion on the surface of sulfide minerals will significantly affect the flotation effect and separation efficiency of sulfide minerals. No matter the flotation speed or recovery, the inert medium is obviously better than the steel ball medium. The finer the grinding particle size, the greater the influence of grinding medium environment on the recovery. The grinding process basically eliminates the influence of iron, which will greatly improve the subsequent flotation operation.
Effect of different grinding media on
flotation behavior of galena
Effect of different grinding media and
grinding time on flotation recovery
Ceramic balls used in ALC mill
Feature 4
The power density of ALC mill is 300kw /m³; The power density of ball mill and tower mill is only 20kW /m³;
Compared with the 50mm grinding media of ball mill, the surface area of φ3mm ball for ALC mill per unit volume is increased by 15 times, and the grinding efficiency is improved.
Feature 5
According to the change of ore supply conditions and product particle size requirements, the mill speed can be adjusted by frequency conversion to ensure the stable quality of grinding products
Feature 6
The guide rail type dismounting cylinder is convenient and quick, and the labor intensity of workers is low. It only takes one shift to change the mixing plate and grading wheel.
Feature 7
The grinding media is 2-4mm ceramic ball, and the cylinder is lined with rubber material. The cylinder is basically noiseless when the equipment is running. The cylinder does not rotate, and the working area is safe and environmentally friendly.
Feature 8
With the same processing capacity, the volume of ALC mill cylinder is less than 20% of that of ball mill, and the floor area is small. The equipment is horizontal, the height is not more than 3m, the height of the plant is low, saving capital investment.
Model | Overall dimensions(mm) | rated power(KW) | Treatment capacity | Grinding fineness P80 particle size(μm) | Grinding media (mm) | Equipment weight (kg) |
1.5L | 240x160x620 | 0.75 | 400 ~ 600g/批 | 5~60 | 0.3-2 | 20 |
5L | 1100x500x1150 | 4 | 45~115kg/h | 5-60 | 1-2 | 300 |
20L | 1510x800x1500 | 22 | 100 ~ 1000kg/h | 15-40 | 1-3 | 900 |
100L | 3950x1000x2030 | 55 | 1 ~ 3t/h | 15-40 | 2-6 | 3200 |
500L | 5860x1350x2460 | 200 | 3 ~ 10t/h | 15-40 | 2-6 | 9200 |
1000L | 8750x1300x1830 | 400 | 30t/h | 15-40 | 3-6 | 10300 |
1500L | 12450x1820x1710 | 560 | 10 ~ 40t/h | 15-40 | 3-6 | 23500 |
3900L | 15200x1850x1850 | 1120 | 30 ~ 100t/h | 15-40 | 3-6 | 34000 |
5000L | 18000x2000x2500 | 1600 | 150t/h | 15-40 | 3-6 | 40000 |
10000L | 20000x2700x3000 | 3000 | 60 ~ 240t/h | 15-40 | 3~6 | 75000 |
Note:
·The voltage of 1.5L ~ 1000 is 380V; the voltage of 1500L ~ 10000l is 10000v or 6000V
;·The treatment capacity refers to the treatment capacity of grinding iron ore when feeding -70% of -200 mesh and discharging 80% of -325 mesh